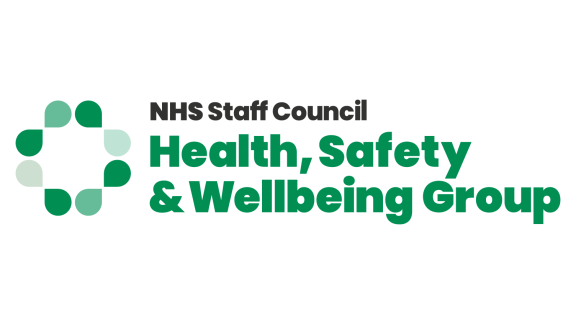
About the Health, Safety and Wellbeing Group
The Health, Safety and Wellbeing Group (HSWG) is a sub-group of the NHS Staff Council. It is a tripartite group involving staff side representatives from healthcare unions, management side representatives from NHS organisations and specialist members, such as the Health and Safety Executive, and the Institute of Occupational Safety and Health with a remit to do the following:
- to raise standards of workplace health, safety, and wellbeing in healthcare organisations
- to promote a safer working environment for all healthcare staff
- to promote best practice across both the NHS and the Independent sector.
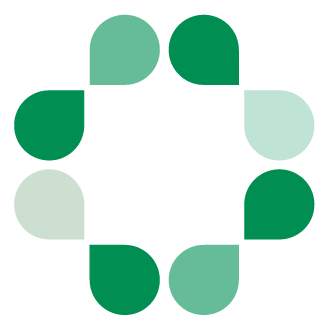
This guidance was produced through partnership working between unions, management and specialist advisors. The group wishes to ensure this guidance is implemented with the same partnership approach. HSWG recognises that partnership working ensures best outcomes for patients and staff in protecting their health, safety and wellbeing.
Other HSWG resources to support you in your organisation can be found here.
Introduction
This guidance aims to help NHS health and safety (H&S) professionals and representatives to review their competency programmes to assess whether managers have the right skills to address health and safety issues effectively.
Managers (particularly front-line managers) play a key role in health and safety. They need to have the right competencies to manage health and safety effectively, including:
- completing risk assessments
- developing, implementing and monitoring procedures
- investigating incidents
- providing appropriate support to staff as required.
Formal training is only part of the process for a manager to be competent in health and safety. Competency is about the balance of training, experience, skill, aptitude, attitude, knowledge and its application.
Competence is clearly outlined in both ISO45001:2018 ‘Occupational health and safety management systems’ and HSE Managing for Health and Safety.
HSWG's guidance on workplace health and safety standards describes the principles which provide the basis of effective health and safety management and should be read in conjunction with this document.
“The essence of competence is relevance to the workplace. What matters is that there is a proper focus on both the risks that occur most often and those with serious consequences.
Competence is the ability for every director, manager and worker to recognise the risks in operational activities and then apply the right measures to control and manage those risks.”
Judith Hackitt, Former Chair, Health and Safety Executive
The competence of managers should not be confused with the legal requirement to appoint a competent person to help you carry out your health and safety duties.
Key competencies overview
The table below illustrates the required key competency areas for managers at each level. Competencies required for employees are also included.
We have used the structure from the HSE’s Managing for Health and Safety (HSG65): Plan, Do, Check, Act.
Competency 1: Understanding of personal accountabilities
Required for:
- Director
- Assistant director/function manager
- Line manager
- Supervisor
- Employee
The Knowledge and Skills Framework (KSF) requires every employee to assist in maintaining a healthy, safe and secure working environment. This is part of the Agenda for Change contract of employment. This competency covers the following points:
- All staff have health and safety (H&S) personal accountabilities. This tends to be the focus of training and development at employee and operational management level.
- An understanding of the law and how it relates to individuals, line managers, assistant directors/function managers and directors is essential, but should also be balanced with a view of the moral and cost arguments for H&S.
- The message that tends to resonate with line managers is the moral association that every employee has a right to work in a healthy and safe environment without the risk of injury.
- Senior managers need to lead on health and safety. They need to ensure that:
- there is a safety culture in their organisation
- staff are engaged on health and safety issues
- health and safety is seen as essential to how work is done, it is an enabler rather than a barrier.
- Training senior managers in carrying out safety tours and expecting these to be done is a good first step to ensuring H&S leadership is visible and matters.
- Employees need to be clear on what responsibilities and accountabilities they have. Responsibility refers to the obligation to undertake a task and adhere to specific policy and procedural requirements. Accountability implies they are answerable for the outcome of a task, activity or deliverable. Organisational policies, together with competency training should ensure clarity between accountability and responsibility in relation to H&S management.
Competency 2: Suitable health and safety management system
Required for:
- Director
- Assistant director/function manager
- Line manager
- The health and safety management system is the means by which an organisation controls risk through the management process (Health and Safety Executive). This needs to be proportional to the risk and ideally embedded in the organisation’s management quality system.
- Directors and assistant directors/function managers need to understand the organisational structure, planning activities, responsibilities, practices, procedures, processes and resources for developing and achieving, reviewing and maintaining the organisation’s Occupational Health and Safety Policy (BSI).
- Health and safety is like any other management process and should follow the ‘plan, do, check, act' process, which directors and assistant directors should be familiar with. Specific awareness of how this relates to H&S management should be covered with directors and assistant directors so that they understand how it fits together.
- Line managers need to know how the health and safety management system relates to them.
For further information, see Section A of the workplace health and safety standards.
Key competencies: Plan
Competency 3: Determining your policy
Required for:
- Director
- Assistant director/function manager
- NHS organisations tend to be very policy-driven. Directors and assistant directors/function managers need to be directly involved in H&S policy development to show leadership and commitment to H&S.
- Policy groups must have health and safety professionals and staff side engagement. Directors and assistant directors/function managers must be involved in the process to effectively set the H&S standard within the organisation and sign-off policy.
- Competency is gained by involvement in the process rather than any specific formal training course.
Competency 4: Planning for implementation
Required for:
- Assistant director/function manager
- Line manager
- Assistant directors/function managers and line managers need to be competent planners. This should be a key core skill for anyone in these posts.
- Training can involve asking line managers to identify where their department is on H&S, using maturity matrices, *safety culture climate tools or reviewing against internal policies. Ask them to produce an action plan to increase performance or address the issues found.
- It is important that any exercises to develop H&S plans are real, followed up and monitored centrally at H&S committees or policy groups by the use of a scorecard system.
- Sometimes the best training can be the production and use of a plan so that it is accepted and shown to be of benefit.
Directors will not be involved in detailed implementation planning but they will need to ensure that adequate plans and resources for implementation are in place.
* Examples of culture climate tools are The Safety Maturity Model and the Safety Culture Maturity Model.
Key competencies: Do
Competency 5: Profiling your health and safety risks
Required for:
- Director
- Assistant director/function manager
- Line manager
- Understand the level and nature of risk and how this fits into the overall risk management and governance structure of the organisation.
- Decide what the priorities are and identify the most significant risks.
- Be aware of how risks are defined and escalated through the organisation to the place where appropriate resources can be accessed or decisions be made.
- Line managers need to understand the importance of working with employees and their H&S representatives to understand the risks in their areas.
For further information, see Section A of the workplace health and safety standards and page 29 of HSE's managing for health and safety.
5.1 Assessing the risks
Required for:
- Line manager
- Supervisor
- Employee
- Risk assessors need to be trained in the organisation’s risk process, which should include the HSE’s 5 steps to risk assessment, but line managers also need to be aware of their role in this process.
- Line managers need to have enough knowledge and understanding of the risk system so they can make informed decisions about risk in their areas and sign off risk assessments. They need to know how and who to escalate risks to when they are unable to action them, for example, due to resource issues.
- Supervisors also need to know how to interpret risk assessments and communicate the hazard, risks and controls in their area.
- Employees may need training in carrying out dynamic risk assessments, for example, in manual handling and lone working situations. They will need to understand the principles of risk assessment and how to apply them in these circumstances.
For further information, see Section A of the workplace health and safety standards.
Competency 6: Organising for health and safety
Required for:
- Director
- Need to have awareness of how the H&S management system is set up and resourced so they can have a view of whether it is adequate and effective.
- Experience of leadership in H&S in previous roles would be expected but no formal training required.
- Assistant directors/function managers will only need to be aware of and involved in the collection of information for directors.
6.1 Control
Required for:
- Assistant director/function manager
- Line manager
- Supervisor
- All need to have proportional knowledge and understanding of the role of supervision.
- Anyone who procures and oversees contractors needs to know the H&S implications and the risks that they import into the organisation, with an understanding of method statements, risk assessments and vetting procedures.
- For supervision, inspection as a safety skill should be understood so that supervisors and line managers can follow the work being done to ensure processes are validated.
- Assistant directors/function managers need to be competent in safety tours.
- Line managers and supervisors must understand issues regarding emergency preparedness and the concept of serious and imminent danger, all staff must know when to stop work and how to move to a safe place.
- Evacuation procedures must be tested and periodically practised, with those in charge receiving extra training and drills.
For further information, see Sections A and M of the workplace health and safety standards, and pages 31/32 of HSE's managing for health and safety.
6.2 Cooperation
Required for:
- Assistant director/function manager
- Line manager
- Supervisor
- Employee
- Assistant directors/function managers and line managers need to understand the benefits of working in partnership with staff and union representatives.
- Where staff are engaged in H&S they tend to have a better understanding of the hazards and risk in their workplaces with greater acceptance of control measures necessary to mitigate the risk. These workplaces tend to have lower accident rates and are therefore more productive.
- An understanding of the basic requirements for facilitation of the role of a trade union safety representative should be enhanced by active involvement in safety committees and day-to-day working.
- Line managers and employees need to understand the role and function of H&S representatives so they can be successfully included in consultation when needed.
- An understanding that when a workplace is shared by more than one organisation, arrangements need to be agreed on responsibilities for managing health and safety in the building(s) and sharing and communicating information on key health and safety issues and risks.
For further information, see Section A of the workplace health and safety standards and page 34 of HSE's managing for health and safety.
6.3 Communication
Required for:
- Director
- Assistant director/function manager
- Line manager
- Supervisor
- Employee
- Two-way communication from the top and bottom of an organisation is vital for H&S, and as such must be understood by all managers.
- The recognition of the importance of behaviours, written communications and face-to-face interaction as a safety skill should form part of all management training.
- Effective communication is when all employees receive, understand and pass on the correct message. How things are perceived is as important as what is said, for example, a weak H&S message is “do this job safely but I want it done tonight” as opposed to a strong H&S message which is “I want this job done tonight but I want it done safely”.
For further information, see Section A of the workplace health and safety standards and page 38 of HSE's managing for health and safety.
6.4 Competence
Required for:
- Director
- Assistant director/function manager
- Line manager
- Supervisor
- Employee
- All levels within an organisation need to show competence in the work that they do. This includes employees being trained in procedures so that they can use the equipment provided in the right way. How people gain competency is a mixture of skills, knowledge and experience gained through a combination of training, practice, coaching and supervision. Competency must be demonstrated and assessed.
- H&S training needs to have objectives, measures and feedback to ensure the learning outcome has been delivered. This can be done through tests but also through practical demonstrations, for example, production of H&S plans, risk assessments or inspection and the associated report.
- Competence starts with the correct selection, recruitment, assessment and training of individuals for jobs and tasks.
- Line managers who carry out selection and recruitment should understand how H&S relates to the job in hand and be proficient at identifying knowledge and skills in others.
For further information, see Section A of the workplace health and safety standards.
Competency 7: Implementing your plan
Required for:
- Assistant director/function manager
- Line manager
- It is important to ensure that assistant directors/function managers and line managers know how to implement their plan. They should put in place the correct controls, ensuring resources, equipment and the maintenance of it is carried out, while staff are trained, competent, instructed and supervised.
- Coaching and mentoring managers and reviewing their performance is key to ensure that they develop the right skills rather relying on fixed training courses.
- Progress against the plan should be documented and may be contained in a quality system or by reference to an H&S standard, such as the Health, Safety and Wellbeing Group Workplace standards or the Occupational Health and Safety Standard ISO45001.
- Documentation must be suitable and sufficient in that it is proportionate to the risk faced, and must be concise, easy to follow and use.
- Training in documentation writing may be required depending on the assessment of the development needs of the individual line manager.
For further information, see page 38 of HSE's managing for health and safety.
7.1 Implementing risk controls
Required for:
- Line manager
- Supervisor
- Employee
- Risk controls will be proportionate to the hazard in terms of likelihood and severity. Safe systems of work will need to be understood by all who carry out the tasks and supervise them for their hazard, risk and controls and may be formally recorded in written procedures.
- If high hazard then a knowledge and understanding of safety systems, such as permit to work, may be required by line managers and employees. It is important to recognise the need to engage in competent technical advice, for example, authorising engineers.
- All employees need to know how to escalate their concerns if risk processes are not followed which could lead to serious and imminent danger.
- When implementing risk controls it is important to ensure all employees are considered, including agency/bank staff, students, volunteers and contractors.
Key competencies: Check
Competency 8: Measuring performance and monitoring
Required for:
- Director
- Assistant director/function manager
- Line manager
- Supervisor
- Directors, assistant directors/function managers and line managers need to know what monitoring system is in place at their organisation and how they receive information and feed back into it.
- Board level contact is important and emphasis must be on timely information as with any business performance metric.
- Active and reactive monitoring needs to be provided to line managers with any definitions and gaps in data clearly understood.
- Active monitoring methods need to be balanced against reactive information on injuries and work-related ill health, such as information on risk assessment completion, inspection reports, other information from H&S representatives and mandatory training completion.
- Line managers and supervisors will also need to know how to feed into monitoring systems for H&S, what the escalation routes are and when to use them.
For further information, see Section A of the workplace health and safety standards and page 48 of HSE's managing for health and safety.
Competency 9: Reporting and investigating accidents and incidents
Required for:
- Director
- Assistant director/function manager
- Line manager
- Supervisor
- Employee
- Employees need to be trained in reporting accidents correctly and in a timely fashion.
- Line managers should facilitate access to accident/incident reporting for staff.
- The reporting of healthcare sharps injuries is now a legal duty and this must be brought to the attention of all employees.
- Line managers must be trained in accident investigation to gather information, analyse data to identify failures and allow them to facilitate learning from incidents.
- Line managers need training on how to identify further control measures or more effective ones.
- Line managers need to know how to access specialist advice and help, for example from their H&S or risk departments.
- Line managers must be aware of what internal escalation processes are required, for example never events* and how to correctly report incidents to the HSE where required by the Reporting of Injuries, Diseases and Dangerous Occurrence Regulations. This may be done by an internal H&S department or be delegated to responsible departmental managers.
*Never events are serious, largely preventable patient safety incidents that should not occur if the available preventative measures have been implemented.
For further information, see Sections A and B of the workplace health and safety standards and page 51 of HSE's managing for health and safety.
Key competencies: Act
Competency 10: Reviewing performance and learning lessons
Required for:
- Director
- Assistant director/function manager
- Line manager
- Practical experience of involvement in H&S review at senior level is best. Allow line managers as part of their development to attend as observers to H&S committees or senior management reviews is key.
- The review must cover outputs which are improvements to the H&S management system that then feed back into the H&S plan.
- Learning lessons and sharing information with H&S representatives in partnership must be understood as beneficial to the H&S management system.
For further information, see Section A of the workplace health and safety standards and pages 54/56 of HSE's managing for health and safety.
Further information
The following guidance may also be useful:
- The Health, Safety and Wellbeing Group's (HSWG) Workplace health and safety standards. The standards provide advice on the training and qualifications required for health and safety managers and advisors.
- HSE guidance – What is competence?
- HSE guidance – Managing for health and safety (HSG65)
- ISO 45001:2018 - Occupational health and safety management systems — Requirements with guidance for use
- HSE/IOD guidance – Leading health and safety at work